Lubricant Analysis Services:
A routine lubricant analysis service helps predict and manage equipment downtime, thereby improving performance uptime. The process involves taking a small sample while the machine is running, testing and monitoring the oil condition to determine maintenance needs. Oil analysis is an essential part of a predictive maintenance strategy, providing information about machine performance and increasing the potential cost savings of your maintenance plan.
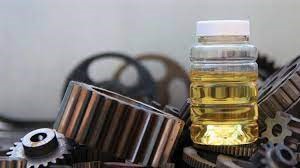
How is oil analysis performed?
Oil analysis methods can cover a wide range of areas and tactics. Key among them are:
• Condition-based monitoring: As a form of condition-based maintenance, oil analysis is a key element in keeping industrial equipment in optimal condition. Manufacturers rely on the information this process provides to monitor the condition of their machinery and identify potential problems before they have a chance to impact productivity.
• Visual inspection for contamination and viscosity: For maximum effectiveness, visual oil inspections should be performed at least daily. These simple inspections can detect the presence of debris, large contaminants, uneven viscosity, and other problems that, if caught early, can be resolved relatively easily (often by simply changing the oil). Visual inspections can also indicate larger equipment wear issues.
• Wear particle analysis: Since the oil is in direct contact with moving parts, this is where debris, no matter how small, is collected as these parts wear. The presence of debris or contaminants indicates the rate of equipment wear and can alert maintenance personnel and equipment operators to early wear issues that indicate abnormal operation that can then be addressed.
Benefits of Oil Analysis
Benefits of oil analysis include:
1. Early detection of unexpected equipment wear, indicating the presence of potential problems in equipment functionality
2. An accurate picture of when oil needs to be changed, so that oil does not continue to operate when it is no longer effective, while ensuring that oil is not changed unnecessarily based on rigid time schedules, thus reducing costs.
3. A deep insight into equipment performance, as oil condition is closely related to equipment efficiency, wear and performance
4. A continuous and ever-expanding data set that enables better maintenance scheduling and decision making, ultimately improving maintenance efficiency and productivity, while reducing maintenance costs
5. Keeping machinery running well to prevent unexpected breakdowns that could endanger employee safety
6. Ensuring equipment operates at peak performance to reduce energy consumption and improve the environmental sustainability of the manufacturer
Why choose our services?
With our experienced team of experts and state-of-the-art equipment, our Oil Analysis results allow you to detect unexpected equipment wear, know when to change your oil, gain a better understanding of your equipment performance and make informed decisions when scheduling lubrication maintenance.
Let us help you improve machine performance and productivity, while reducing maintenance costs.